High Current Rectifiers Application
- IGBT BASED RECTIFIERS
- POLARISATION RECTIFIERS
- FLOAT CUM BOOST CHARGER
- ELECTROCHLORINATION
- ELECTRO CHEMICAL APPLICATION
- ELECTROPLATING
- ANODIZING
- ACVR PANELS
- SCR CONTROLLED FURNACE POWER SUPPLIES
- TEMPERATURE CONTROLLER PANELS
GE TEK Make Modular IGBT switch mode rectifiers are designed to give best electrical performance fro electroplating/Anodizing process and get excellent platting quality.
These rectifiers are modular design, reducing user's power consumption and integrated with timer control and RS485 communication interface.
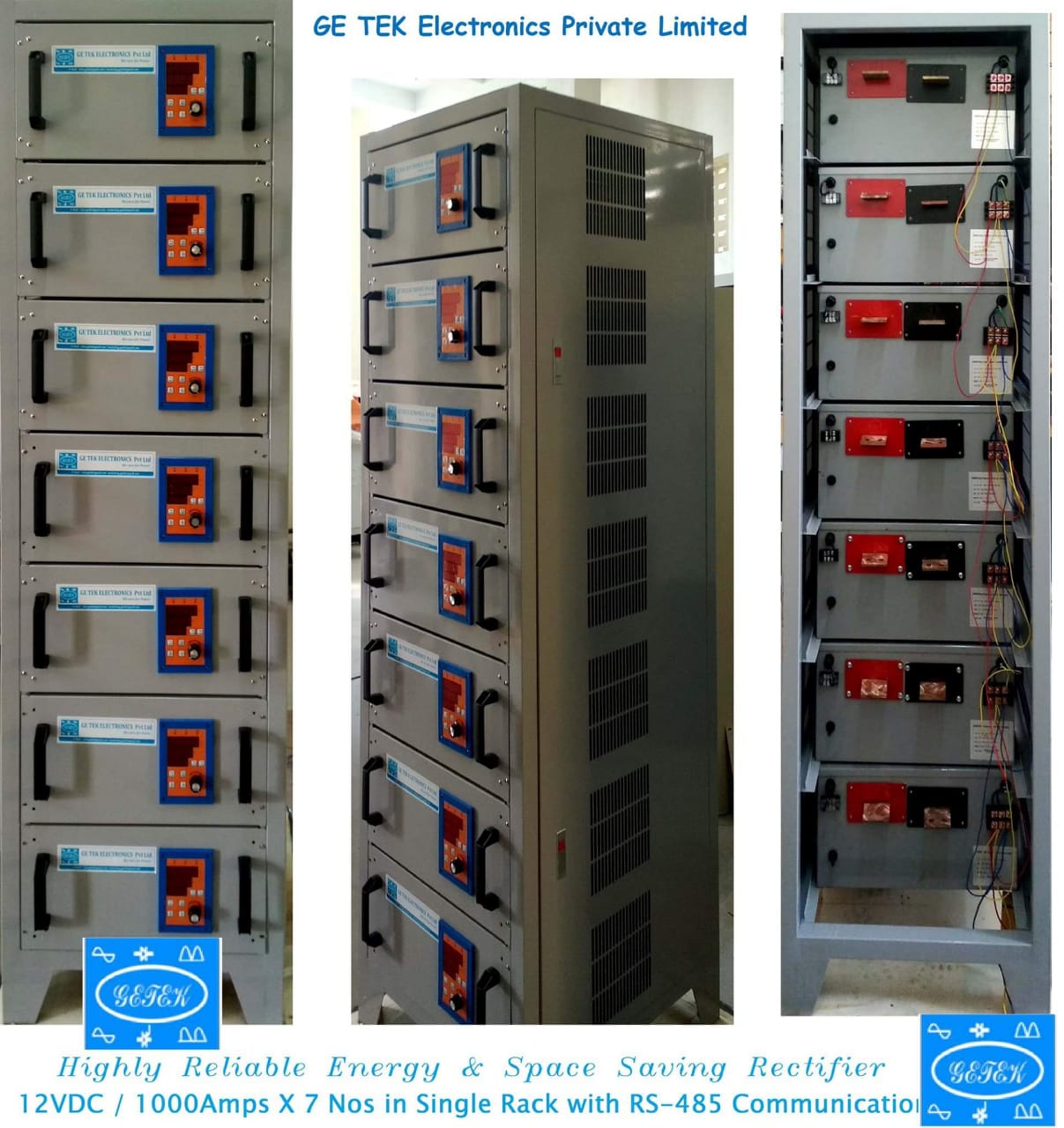
Technical Data:
- Rectifier Type - IGBT High Frequency Modular Structure
- I/P Voltage - 380-440VAC 3 Phase 50Hz
- O/P Voltage - 6V-200VDC
- O/P Current - 10A-10KA
- Control Accuracy - ≤± 0.5%
- Power Factor - ≥ 0.98
- Efficiancy - Better than 90% at rated Output
- Control Mode - Constant Voltage/Current
- Cooling - Forced Air/ Water Cooling
- Protections
- Output Over current protection
- Short Circuit protection
- Over Heat Protection
- Input Over/Under voltage protection
Optional Facility:
We can provide touch screen type HMI for programming the plating cycle. Programming facility is available up to 15 different models and each model can have 30 steps.
Chemical Processes often have large power rectifiers as their primary source of DC Power. If these rectifiers are turned off, either for maintenance or a malfunction, there is a danger to the hardware of the chemical process. To solve this problem, standby rectifiers are installed in parallel with the main rectifiers. These rectifiers, known as Polarization Rectifiers, pass electric current through the process and prevent damage. As these rectifiers are used as stand by, they have to be extremely reliable.
During start-up of the electrolyser, as the main rectifier is off, the PR supplies current to the electrolyser, and continues to supply the current as long as the output voltage of the main rectifier is less than the voltage of PR. The moment the main rectifier voltage is equal to the PR, the PR supplies current equal to or less than the set point current During normal operation this unit operates in parallel with the main rectifier supplying rated current each polarization rectifier consists of 2 rectifiers which are designed to operate in parallel redundant mode, A third rectifier known as the Booster rectifier may also be used.
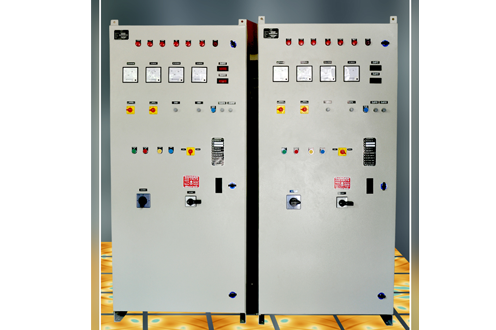
Special Features of our Polarization rectifiers
- Auto / Manual
- Output short circuit proof
- In build power factor correction and harmonic filter
- AC input overload protection
Our design Ratings:
- 50V/300A
- 110V/75A
- 220V/50A DC, 220V/75A DC
- 420V/60A DC, 420V/75A DC
- 500V/75A DC
POWER HOUSE FCBC designed to supply continuous power to the DC load and simultaneously charge the batteries connected. Input supply from 415 VAC 3 Phase or 230 VAC 1 Phase is converted to regulate DC. The charger has two independent systems (Float and Boost), Normally the DC power is supplied to the load by the Float Charger. It also supplies trickle current to the battery to keep it healthy. If the charging current under Float Mode exceeds a set level, Boost charger is switched ON. It supplies Quick charging current to the battery. On battery reaching the set value, the Boost Charger is switched OFF.
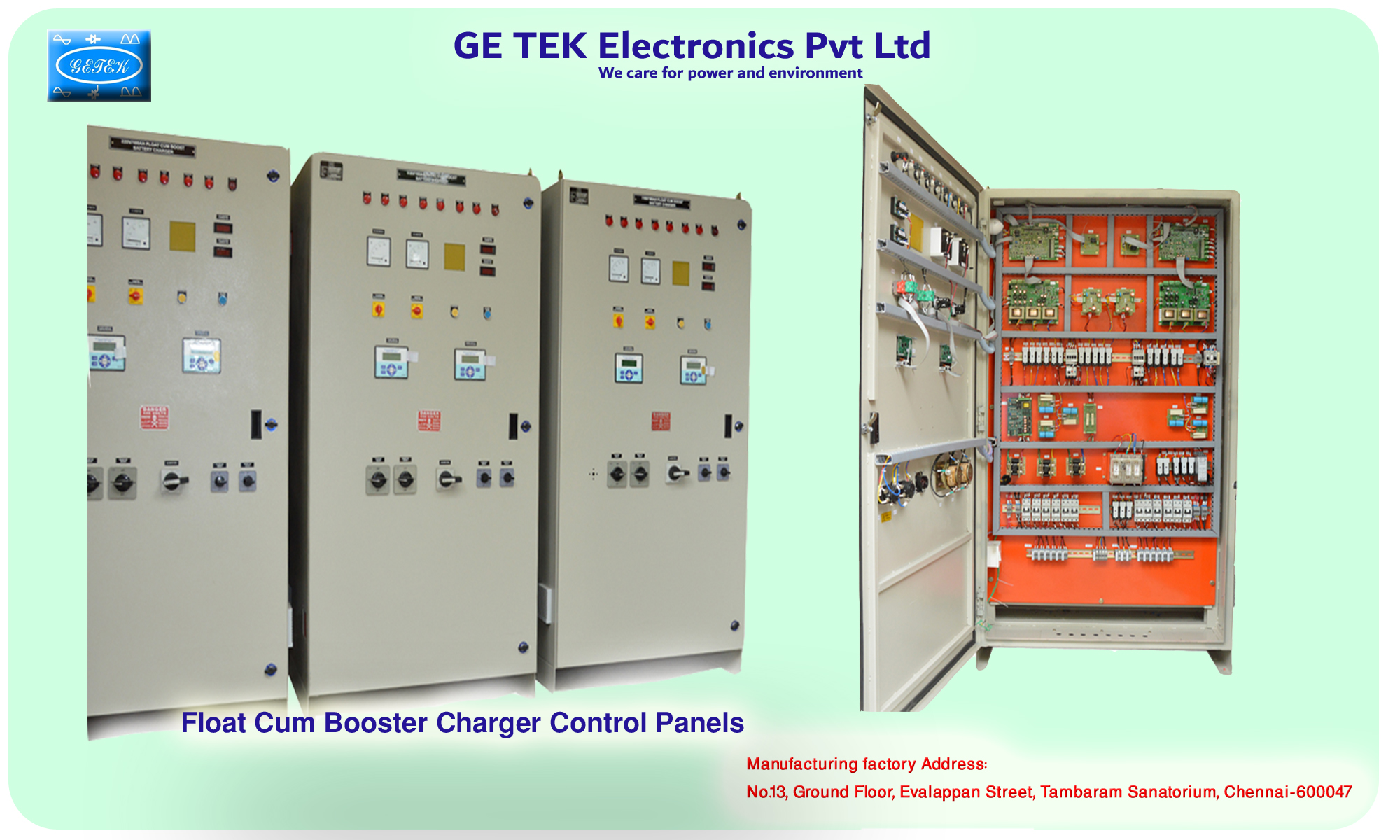
Process of disinfection and anti-fouling; effectively converts a sodium chloride solution to sodium hypochlorite (bleach) utilizing either a combination of fresh water, salt and DC power, or a combination of sea water and DC power.
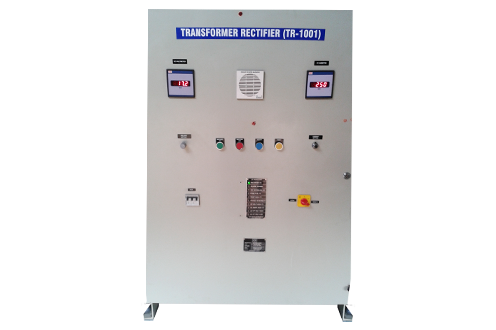
Electrochemical Plants require low voltage (ranging from 5VDC to 1000VDC) and high current (From 250ADC to 30,0000ADC or more) DC sources. Continuous process applications like hydrogenation, electrolysis, chlorination, Potassium & Sodium Chlorate, Soda-ash, Caustic chlorine Production, Copper, Aluminium, Zinc refining etc., reliable DC sources. GE TEK Electronics Private Limited is offering highly reliable Rectifiers for continuous process industries at economical cost. GE TEK Electronics Private Limited is offering consultancy for selection of optimum high current rectifiers.
Electro deposition of a metal (or metal alloy) from an electrolyte solution onto another component. The item to be plated (substrate) is connected to the cathode. Direct current (DC) is sent through the anode. The process of coating an item (substrate) with a metal by means of electric current
Process of coating primarily aluminum, titanium and magnesium through theuse of an anodic circuit. Produces a thin film of aluminum oxide on the aluminum part. A variety of colors are available in aluminum anodizing through subsequent dye processes and in titanium/magnesium anodizing through voltage control
GETEK make AC voltage regulator panel for Aluminium colouring applications.
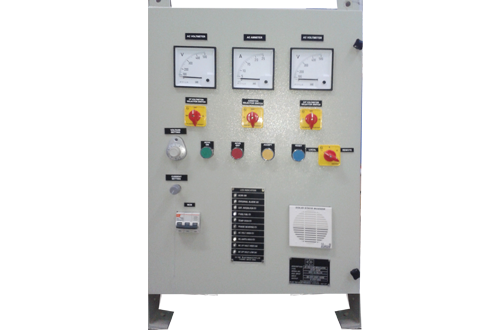
High power silicon controlled rectifier systems became available and those systems also found their way into the furnace boosting control systems. The main advantages of SCR (Silicon Controlled Rectifier) controlled systems are of course that they are based on solid state technology and will show no signs of wear, that they are continuously controllable and that they are capable of very precise.
Temperature and process controllers are used over a vast range of industrial, scientific and commercial applications. These controllers automatically adjust outputs based on sensor feedback working in concert to control process variables such as temperature, flow, pressure and relative humidity, as well as, to achieve an optimized and stable process.
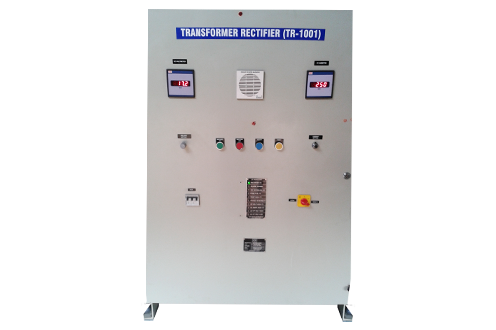